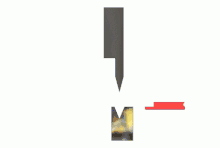
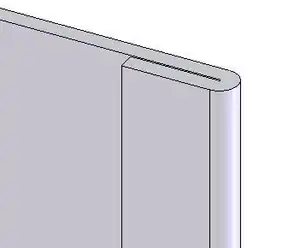
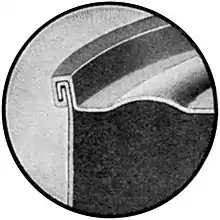
Hemming and seaming are two similar metalworking processes in which a sheet metal edge is rolled over onto itself. Hemming is the process in which the edge is rolled flush to itself, while a seam joins the edges of two materials.[1]
Hems are commonly used to reinforce an edge, hide burrs and rough edges, and improve appearance.[1]
Seams are commonly used in the food industry on canned goods, on amusement park cars, in metal roofing (with a roof seamer), and in the automotive industry.
Process
The process for both hemming and seaming are the same, except that the tonnage (amount of force exerted) requirement is greater for seaming. The process starts by bending the edge to an acute angle. A flattening die is then used to flatten the hem.[1]
Types
There are two types of hemmed edges: closed hems and open hems. Closed hems are completely flush while open hems have an air pocket in the bend. The major difference is that the tonnage required for a closed hem is much greater than that for an open hem.[2]
Material thickness [mm] | Open hem | Closed hem |
---|---|---|
0.6 | 9 | 23 |
0.8 | 12 | 32 |
1.0 | 15 | 40 |
1.2 | 17 | 50 |
1.6 | 24 | 63 |
2.0 | 30 | 80 |
2.6 | 55 | 90 |
3.2 | 70 | 100 |
4.5 | 105 | 200 |
See also
References
- 1 2 3 Benson 1997, p. 137.
- 1 2 Benson 1997, p. 138.
Bibliography
- Benson, Steve D. (1997), Press brake technology: a guide to precision sheet metal bending, SME, ISBN 978-0-87263-483-1.
Further reading
- Drozda, Tom; Wick, Charles; Bakerjian, Ramon; Veilleux, Raymond F.; Petro, Louis, Tool and manufacturing engineers handbook: Forming, vol. 2, SME, p. 4-9, ISBN 0-87263-135-4.