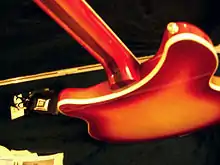
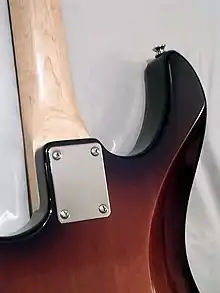
A set-in neck (often shortened to set neck) is the traditional form of joining the neck of a stringed instrument with its body. This is typically done with a tightly fitted mortise-and-tenon or dovetail joint, secured with hot hide glue. Among its qualities are a warm tone, long sustain, and a large surface area to transmit string vibration, leading to a "live" feeling instrument. In guitars it also often allows superior access to top frets closest to the body.
It is a common belief that this yields a stronger body-to-neck connection than an inexpensive mechanically joined bolt-on neck, though some luthiers believe a well-executed bolt-on neck joint is equally strong and provides similar neck-to-body contact. However, neither of these joints is as strong as a neck-through construction, the third of the common methods of neck attachment, which requires more material and is usually found only on high-end solid body guitars.
Set-in necks are the most popular on acoustic guitars. Almost all major acoustic guitar manufacturers (notable exceptions being Taylor Guitars, Godin Guitars, Collings Guitars) use set-in necks and have applied this method also to their electric guitars, for example Gibson. With hollow body set-in neck electric guitars of the 1940s being rather expensive to buy and repair, newcomer Fender in 1950 introduced electric guitars that were easier to manufacture, combining a simple solid body with a bolt-on neck. Fender also introduced the electric bass guitar by adding a longer neck bolted to a solid guitar body.
In rare cases, makers use other solutions. Babicz Guitars makes a mechanically joined neck that can be "wound" up or down to adjust action height.
Glue
Set-in necks are traditionally and best secured with hot hide glue - which may be re-heated to allow convenient disassembly. White and yellow PVA glues are inferior alternatives. Use of Epoxy or Cyanoacrylate is not recommended as disassembly is then no longer possible.[1]
Advantages
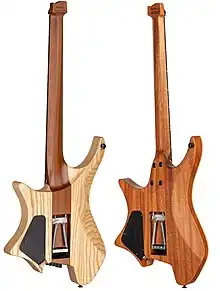
Typically cited advantages of set-in neck include:
- Warmer tone (acoustic guitars only)
- More sustain (acoustic guitars only)
- Often, better access to top frets compared bolt-on necks that use a square metal plate
- Because the increased surface area results in more transmission of strings vibration, set in necks can feel more "alive" than if bolted on.
Disadvantages
- Certain models seem prone to neck breakage - though this may be due to weaker neck wood (mahogany instead of maple).
- Harder and more expensive to mass manufacture than bolt-on necks
- Harder and more expensive to repair or service because the glue must be steamed or melted with a hot knife
- No control over the neck-to-body angle; changing it requires a luthier to disassemble and re-glue the neck.[2]
References
- ↑ Glue comparison chart at frets.com
- ↑ "How To Set a Guitar Neck". GuitarSurf. 2021-09-08.
External links
- Glue comparison chart at frets.com